Stephen P. DeHoff, Jay Z. Yuan, Clinton A. Haynes and Andrew W. Gordon
Stress Engineering Services, Inc., 7030 Stress Engineering Way, Mason, OH 45040
Abstract
2011 brought the introduction of a highly innovative sustainability package in the form of a molded pulp bottle enclosing (Molded-pulp bottle disrupts laundry detergent catagory) a plastic bag in the place of traditional plastic bottles. Structural testing (top load and drop impact) and should-cost analysis find cost opportunities with today’s should-cost analysis (mckinsey.com) of the package against equivalent HDPE bottles suggest that the traditional plastic bottle remains superior to the molded pulp bottle. However, it is possible that more refined engineering(Award-Winning ProForce Package Cuts Development Time by Eight Months) and economic studies could make such a sustainability innovation able to fully achieve its objectives and bring it much closer to (and ultimately exceed) its traditional counterpart in both performance and cost.
Introduction
Sustainability continues to fuel innovation in rigid packaging. Although the precise definition of “sustainable” has been the subject of debate, the drive for more innovative ways of delivering cost-effective sustainable packaging continues to grow. With early efforts aimed primarily at reducing the amount of plastic resin used, other methods of achieving more sustainable packaging, such as renewable-source and biodegradable resins are also making headway.
In 2011 one of the more innovative concepts for sustainable rigid bottle package structures was introduced, molded pulp fibers (Figure 1). This type of packaging was initially targeted at the liquid laundry detergent market.
The liquid containment in the molded pulp bottle is achieved via the incorporation of a low-density polyethylene (LDPE) ‘bag’ within the enclosed volume of the external pulp shell. A conventional drain-back-style closure is used to seal the package and meter flow during use by the consumer.
‘Conventional’ bottles in the liquid laundry category are molded of high-density polyethylene (HDPE) and also incorporate a drain-back closure (Figure 2).
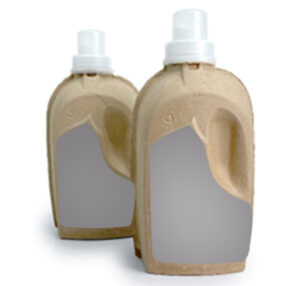
Figure 1. Examples of molded pulp bottles
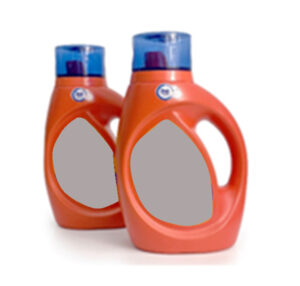
Figure 2. Conventional HDPE liquid laundry bottle
Although full lifecycle effects have not been investigated in this document, on the surface the molded pulp bottle seems to offer a significant sustainability advantage relative to its traditional HDPE counterpart. Whatever, the scales of sustainability (and total delivered cost), HDPE vs. molded pulp will be significantly impacted by the quantity of packaging materials required to deliver the liquid detergent in an undamaged state, to the end user…the consumer. To that end, SES conducted a ‘scoping’ study to evaluate and compare the primary structural attributes of a 50-fluid-ounce molded pulp bottle and a 50-ounce HDPE bottle and estimate the relative cost difference between them.
One full, unopened six-bottle case of each type of package was purchased through a local grocery store for structural performance testing and economic evaluation. Unfortunately, the first case of the molded pulp bottles arrived damaged and leaking with the case saturated with liquid detergent. The damage apparently occurred during transport to the store. A second case was ordered, which arrived undamaged.
Structural Performance Testing
Samples of both bottle types were subjected to common fluid-filled bottle testing procedures to enable comparison. The tests were selected to represent some of the more extreme boundaries of required bottle performance.
The specific tests included:
- Top load after 24 hours of conditioning at 100F, 90% Relative Humidity
- Drop test from 36” after 24 hours of conditioning at 100F, 90% Relative Humidity
The comparison also included an estimate of package economics.
Top Load Testing
Conditioned and tested at 100F and 90% Relative Humidity (RH) to understand storage limit conditions, the molded pulp bottles failed around 11 lbs. during the top load test (Figure 3) A room temperature, 40% RH test was also conducted which resulted in improved top load, about 15 lbs. The top load test followed the standard test procedure (ASTM D642, ISO 12048) with a crosshead speed of 0.2 inch/min. HDPE bottles that were tested under identical conditions failed at about 70 lbs., which is fairly typical for bottles of this type and weight. The pallet load safety factor (PLSF), which provides a rough estimate of the ability of unit loads to survive typical load conditions during warehousing and transport was calculated for each package type using these data. The molded pulp bottle is well below PLSF=1 while the HDPE PLSF was about 2 (Figure 4). This suggests that the molded pulp bottle has to rely heavily on its secondary corrugate case to support the stacking load. Based on this finding Stress Engineering tested the corrugate case that each product was shipped in, per TAPPI standard T804.
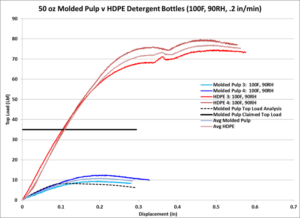
Figure 3. Top Load Load-Displacement Curves
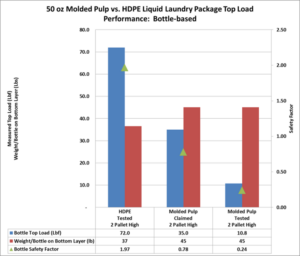
Figure 4. Bottle-Based Top Load & Pallet Safety Factor
As would be expected, the molded pulp bottle shipping case is substantially stronger than the case used for the HDPE bottles. Also conducted at 100F, 90% RH, the molded pulp bottle case failed at about 600 lbs. while the HPPE case failed at slightly less than 300 lbs.
Based on these data and assuming identical pallet patterns and two pallets high stacking, both the molded pulp and the HDPE packaging systems (primary plus secondary packaging) provide sufficient calculated safety factors (Figure 5).
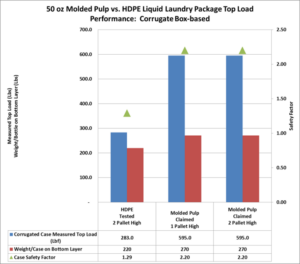
Figure 5. Case-Based Top Load & Pallet Safety Factor
There is a significant difference in top load capacity between the molded pulp bottle and its HDPE counterpart (11 lbs. vs. 70 lbs.). Little performance improvement was found for lower humidity conditioning. Matching the top load performance of the HDPE bottle is a tall order for the pulp-based bottle. However, it is believed that optimizing the geometry of the pulp bottle could result in a measurable narrowing of the performance gap between the two packages. It is observed that the molded pulp bottle fails at the shoulder during the top load testing (Figure 6). SES believes structural optimization of this area of the pulp bottle could yield improved top load performance. Figure 6b illustrates the structural analysis of the pulp bottle when subjected to a compressive top load to failure. (Note a representative material failure model was used in this simulation). The HDPE bottle has an optimized shoulder design forcing the buckling load higher and to a lower position on the bottle. (Figure 6).
A predictive computational structural model of the molded pulp bottle was developed and the top loading of the bottle simulated to gain additional understanding of the underlying structural behavior. The analysis indicates high-stress concentrations occur at the shoulder of the pulp-based bottle which causes the bottle to collapse at the shoulder of the package (Figure 6). Modifying the shoulder design that eliminates the stress concentration would increase the bottle top load capacity. Allocating more material into the high stressed areas (i.e. thicker wall thickness) is another option to strengthen the shoulder for top load, but would likely be much less efficient than a modification to the shape. Predictive computational methods, such as those illustrated in Figure 6 can be used to optimize both the shoulder geometry and wall thickness (to the extent possible) without the need to execute trial and error testing of prototypes.
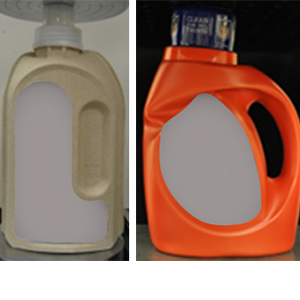
Figure 6a. Top Load Buckled Mold Shapes
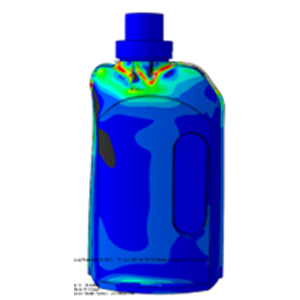
Figure 6b. Predicted Post-buckled Shape of Molded Fiber Bottle.jpg
Drop Impact Testing
A drop test from 36” was conducted for each of the two types of bottles. One bottle each was dropped on its bottom flat, as well as bottom corner. As before, the bottles were pre-conditioned at 100F and 90%RH.
On the bottom corner drop, both the pulp and HDPE bottles survived with physical damage, but no leakage (Figure 7).
On the flat bottom drop, the molded pulp failed dramatically as the LDPE bag seams failed when the heat-sealed seam ‘unzipped’ (Figure 8).
For the bottom drop, the failure of the molded pulp bottle with the LDPE inner liner performs very similarly to that of other flexible containers for which Stress Engineering has provided package improvement services.
Regarding side seam failures specifically, rupture strength at or near the seal bar is a well-known issue in the flexible packaging industry. Seal jaw design, sealing temperature, well time, and pressure are the four key elements that must be ‘managed’ to optimize seal performance and the bag’s rupture strength. Predictive computational methods can be used to simulate the sealing process with the goal of optimizing the design of both the equipment and process, without having to complete endless trial-and-error experimentation on the packing line (Figure 9).
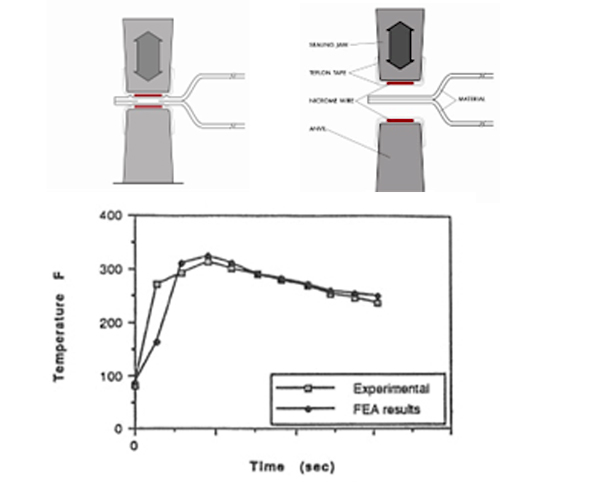
Figure 9. Validation: A comparison of measured and predicted heat sealing simulation results.
Should-Cost Analysis
Economics is necessarily a part of some, but not all, sustainability definitions. An unaffordable package that contributes to not staying in business is not sustainable.
The HDPE package used in this investigation is the least expensive system with an estimated cost of slightly under $0.70 per bottle to the local retailer distribution point (not the local store). The molded pulp bottle is estimated to be about $0.78 per bottle. Part of this advantage to HDPE is associated with finished product pallet fit. The specific bottle sizes and configurations result in HDPE placing about 200 more bottles on a finished product truck inside the 80,000 lbs. weight limit. This portion of the advantage could arguably be erased by more attention to package design details for the molded pulp bottle.
Weight comparisons are also of interest. The actual measured weight of the molded pulp bottle is 40g on average, a reduction of 60% compared to the HDPE bottle.
The heavier, more expensive corrugate case required for the molded pulp bottle (to achieve two high pallet stacking) is about twice the cost of the HDPE case. The board structures are very different. The molded pulp bottle requires 117g of corrugate per bottle (6 per case) while the HDPE package requires 83g (also 6 bottles per case). The board ECT (Edge Crush Test) strength is 40 lbs. for the HDPE bottle and 56 lbs. for molded pulp bottle. In addition, the molded pulp bottle uses weight-bearing partitions between the bottles inside the box (Figure 10).
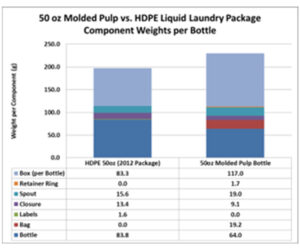
Figure 10. Measured component weights for the molded pulp and HDPE bottles.
Packaging costs are generally raw material weight & cost driven. Raw materials generally are 40-50% of the packaging component price. In some situations the raw material costs can be as high as 60% to 70%. Given this, it’s reasonable to believe that package cost will follow the total raw material content. The advantage here lies with the HDPE package by about 16%. The total package system weight, including corrugate per bottle, is 230g for HDPE and 198g for molded pulp (Figure 10).The cost is also estimated based on the freights and component weights. The comparison of the two package systems is shown in Figure 11. The advantage of the HDPE bottle over the molded pulp bottle is about 12%.
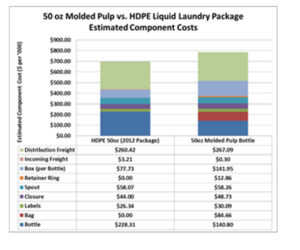
Figure 11. Estimated packaging component cost.
Conclusion
Based on the results of this limited-scope investigation, the molded pulp bottle significantly underperforms the HDPE bottle, its traditional counterpart, in terms of structural performance. The bottle is noticeably weaker in both top load-bearing capacity and drops impact resistance. In addition, the bottle is estimated to be more costly, on the order of 10%, in a fiercely cost-sensitive market. Yet, the molded pulp bottle is a substantial sustainability innovation. It is SES’s opinion that such an innovation does not have to come with such a severe penalty on the bottle’s structural performance and cost. It is likely that more refined engineering and economic studies could make such a sustainability innovation able to fully achieve its objectives and bring it much closer to (and ultimately exceed) its traditional counterpart in both performance and cost.
References
- Seventh Generation website materials; www.seventhgeneration.com
- Ecologic “eco.bottle” line specifications, www.ecologicbrands.com
- “Awards Honor Innovation”, Plastics News, August 14, 2012
- “Molded Pulp Bottle Disrupts Laundry Category”, Packaging World, August 2011.
- “Seventh Generation Bottle Made of OCC and ONP”, www.greenerpackage.com
- “Carbon Labeling and Tesco”, www.tesco.com, 2008
- G. Van Hoof, T. Feijtel, “Comparative Life-Cycle Assessment of Laundry Detergent Formulations in the UK”, Tenside Surf. Det. 40, 2003
- HDPE, LDPE, PP CO2 Data, “Cradle to Gate Life Cycle Inventory of Nine Plastic Resins and Four Polyurethane Precursors”, American Chemistry Council & Franklin Associates, http://plastics.americanchemistry.com/Education-Resources/Publications, August 2011
- Unbleached corrugate, molded pulp CO2 Data, Wal-Mart Scorecard Metrics, 11/10/08
- “Emission Facts: Average Carbon Dioxide Emissions Resulting from Gasoline and Diesel Fuel”, Environmental Protection Agency, February 2005
- ASTM Standard D642 “Determining Compressive Resistance of Shipping Containers, Components, and Unit Loads”
- ISO Standard ISO 12048 “Packaging – Complete, filled transport packages – Compression and stacking test using compression tester”
- TAPPI Standard T804 “Compression testing of fiberboard shipping containers”
- ABAQUS version 6.10. The Abaqus Software is a product of Dassault Systèmes Simulia Corp., Providence, RI, USA.
Ref: W001-SP-Sustainable Bottle Design-Molded Fiber vs HDPE
Keep in touch with us.
Sign up for our newsletter.