Jay Z. Yuan, Clinton A. Haynes, Steve DeHoff, Rich Chomik
Stress Engineering Services, Inc.
At an April 2008 sustainable packaging event, the head of sustainable packaging for a major global corporation told the attendees sustainability will be the packaging topic for the next decade. He was right! Sustainability has become one of the most important global topics and has become a central theme of the packaging-related engineering services for Stress Engineering, and its wholly owned affiliates, Force-4 (www.force-four.com), a product development organization and ALOE Group (www.aloegrp.com),its engineering logistics organization.. This paper describes how predictive, digital computational methods and physics-based testing are being used to achieve sustainability goals by enabling the optimization of the complete packaging system to achieve acceptable performance while minimizing the amount of material used in primary, secondary and tertiary packaging.
Sustainability 101: Understand the Life Cycle Studies
One of the most important tenets of sustainability is to use the minimum amount of material from the start. In general, the packaging system that delivers a product to the consumer with the least total weight of packaging material is the most sustainable. For a traditional packaging system with a rigid plastic bottle as the primary package and a corrugated container as the secondary package, there is a trend to replace the corrugate container with a shrink-wrapped tray, light-weight plastic bottle in a stretched wrapped unit load. This packaging system trend has become increasingly popular (see Figure 1).
However, the trend toward tray-based packaging for purposes of sustainability is not without controversy. It is obvious that a shrink-wrapped water bottle tray will not stack on a pallet with the same stability as a full corrugated container. To achieve parity in performance, more than likely the tray-based system will require additional corner posts and/or stretch wrap to compensate for the differences in stiffness, strength, and stability. Many public domain life cycle studies that have been published allow package performance to vary across the package options that are being compared, relative to sustainability (i.e., Packaging system performance is not considered as part of the life cycle analysis). This approach is wrong. For example, if a pallet is leaning as a result of the distribution/transportation process, it may be rejected by retailers that have automated pallet handling systems in their DC. It is not uncommon for entire trailers of products to be rejected for this reason. Failure to account for the packaging system performance differences can lead to questions about the legitimacy of some Life Cycle results. Another example is damage to the primary package., In a tray-based pallet the primary plastic packaging, a bottle, is more prone to denting since they are exposed to external loads, such as pre-tension of shrink wrap, tightness, pattern, and number of revolutions of stretch films, stacking load, side compression load and incidental side impact load from transportation, etc. (Figure 2).
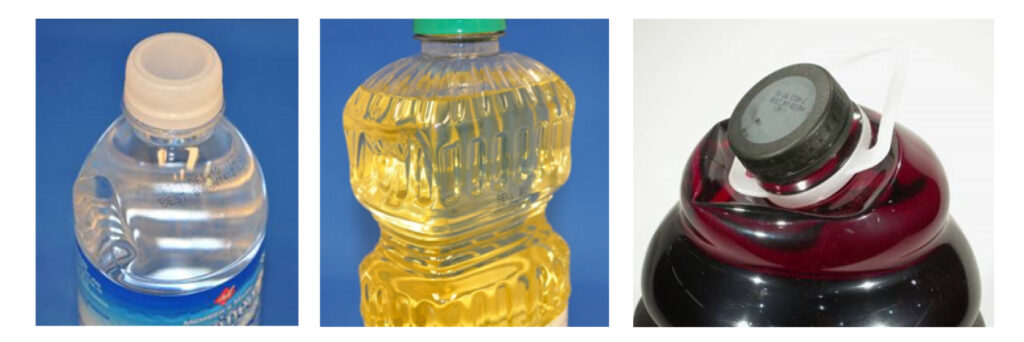
Figure 2. Dented/damaged primary package examples
Although denting may not cause a tray-based pallet to be rejected when delivered as the case of a leaning pallet might, denting is traditionally characterized as damage making the product unsaleable.
As the amount of plastic in rigid plastic packaging is continually being reduced as part of sustainability programs, their ability to survive primary and secondary forces that act on them during their functional life becomes more challenging. Primary loads are generally considered top load and drop impact, for example, whereas secondary loads are those that occur during filling or labeling. Historically, most attention is paid to primary loading, however, as light weighting continues the role of secondary loading survival is emerging as equally important.
Tray-based Packaging
As system-level sustainability and cost-reduction programs advance, new loading mechanisms and forms of critical damage have arisen, one of those being denting damage in tray-based packaging systems. Although tray-based packaging is not new, with early examples appearing in the mid-1980s, it is now the rule rather than the exception. Early adopters of tray-based technology did not experience the level of damage that is experienced now because frequently more plastic was added to the package to compensate for the reduction protection from the corrugated. That is not the situation in current packaging strategy focused on achieving a sustainability objective.
One of the most challenging issues for tray-based packaging is that primary package denting and/or buckling damage has emerged as a new a primary loading scenario that must be addressed. In a conventional packaging development process this problem typically does not surface until line trials and shipping tests are conducted, which are scheduled in the late stages of the development cycle when production bottles are available in sufficient quantity. Discovering a denting problem this late in the project negatively impacts the project schedule and budget.
Predictive Digital Twins of Packaging Systems
Early detection of the potential damage that can be caused in the primary plastic package in a tray-based unit load is crucial to the success of the package development process. To that end, physics-based predictive modeling and simulation methods have been developed to predict the response of a particular package and/or packaging system design to primary and secondary loading. It is no longer necessary to wait until the line trials and ship tests to identify the problems. Modeling and simulation can be used to predict performance long before prototypes exist. This approach enables the packaging engineer to avoid late development failures and rework and deliver packaging systems optimized for sustainability.
Tray-based Packaging System Performance Simulation: Example
This case study illustrates the use of predictive modeling and simulation to predict damage caused by:
- Shrink wrap compression
- Stretch wrap compression or clamp truck compression
- Stacking load
- Dynamic load during transit
The primary package evaluated is a 48oz PET bottle. The packages are shrink-wrapped in a tray (3 x 5) and the trays are stacked in an alternating pattern; 6 layers high on a pallet. The unit load is stretch-wrapped and stacked 2-high in the warehouse at ‘room temperature’ and 1-layer high in transit (Figure 3).
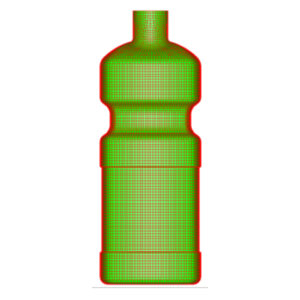
Figure 3a) Digital model of 48oz PET bottle
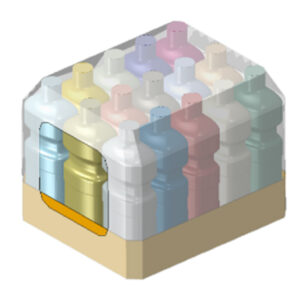
Figure 3b) Filled and tray-packed 48oz PET packages in tray
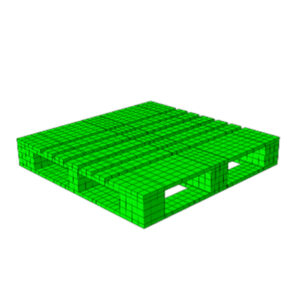
Figure 3c) 40’x48’ wood pallet model
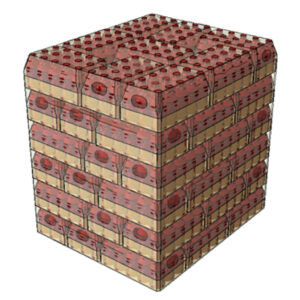
Figure 3d) Computational digital twin of stacked and stretch-wrapped unit load
Figure 3 A predictive digital twin of primary, secondary, and tertiary elements of a packaging system.
Data Required to Construct the Computational Digital Twin
Completing an analysis requires the following input information:
- Material true stress-strain curves (bottle PET, tray, shrink/stretch wraps and wooden pallet) (Figure 4)
- Bottle fill temperature, fill level and filling facility altitude (Figure 5)
- Coefficient of friction (COF) between all interacting components (Figure 6)
- Shrink and stretch wrap compression load (Figure 7)
- Transit vibration (Figure 8)
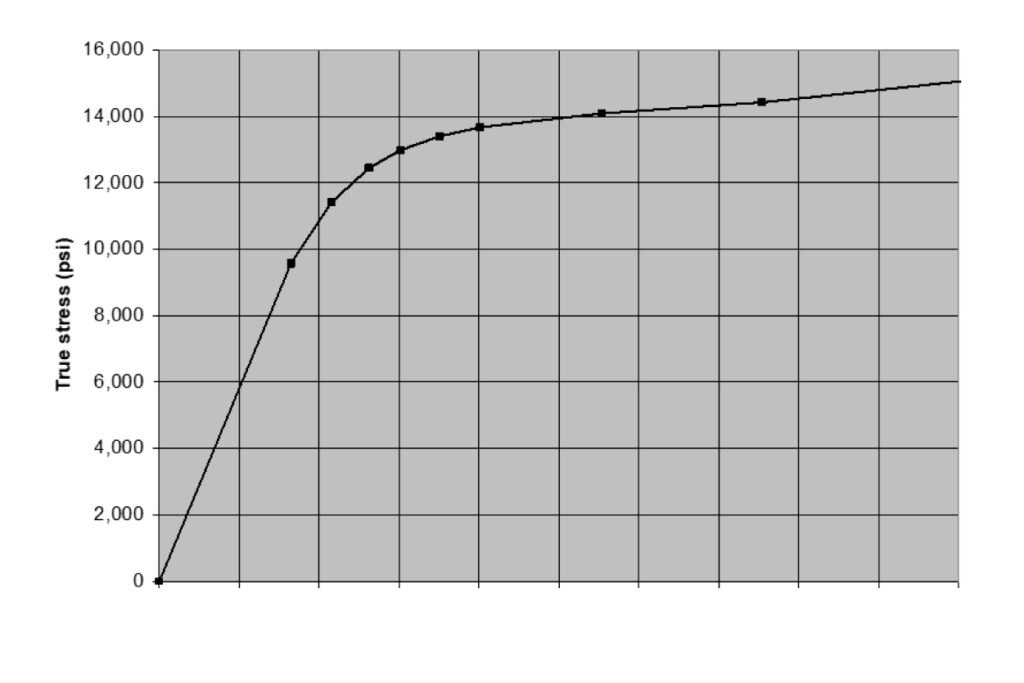
Figure 4a) Bottle PET material true stress vs. true strain curves at room temperature
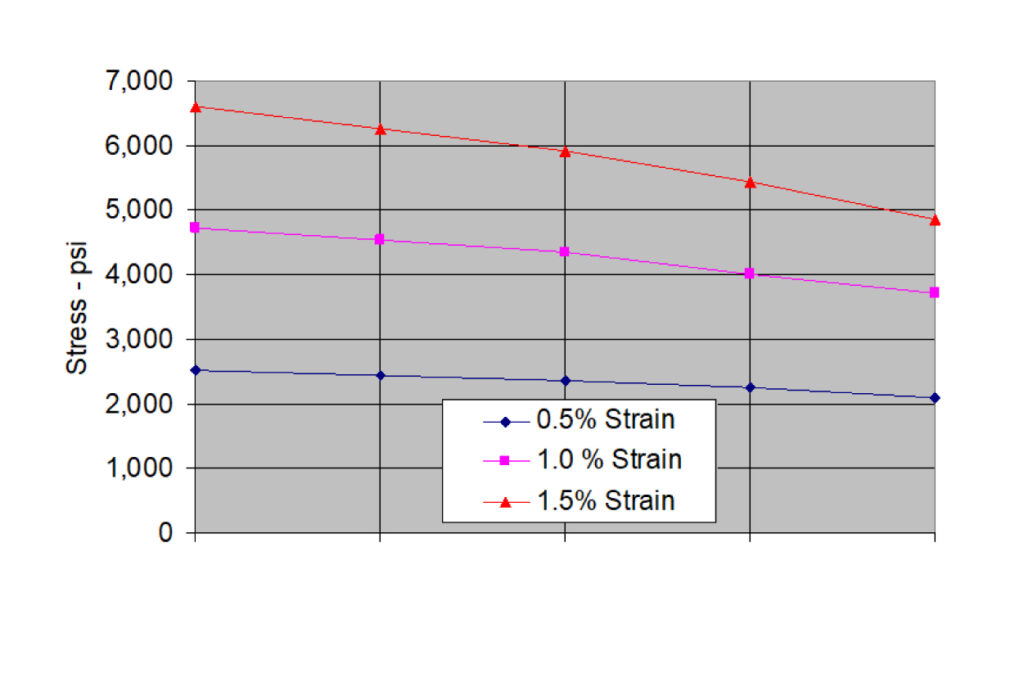
Figure 4b) PET Tensile creep data at room temperature
Figure 4 Bottle PET material true stress vs. true strain curve and creep data at room temperature to predict package short-term and long-term performance
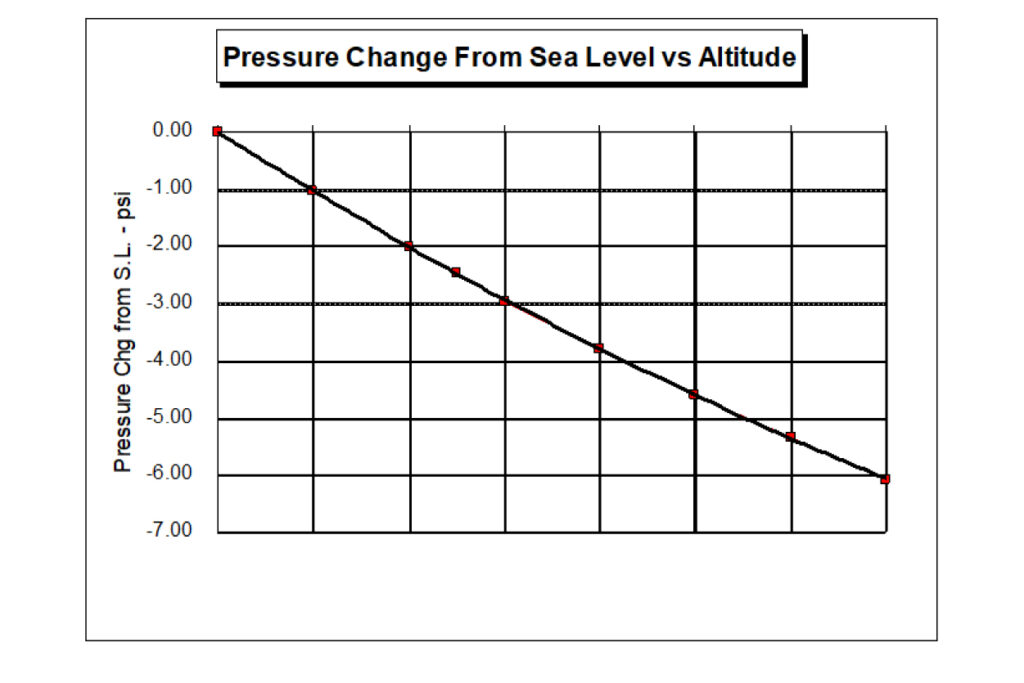
Figure 5a) Pressure change from sea level vs. altitude
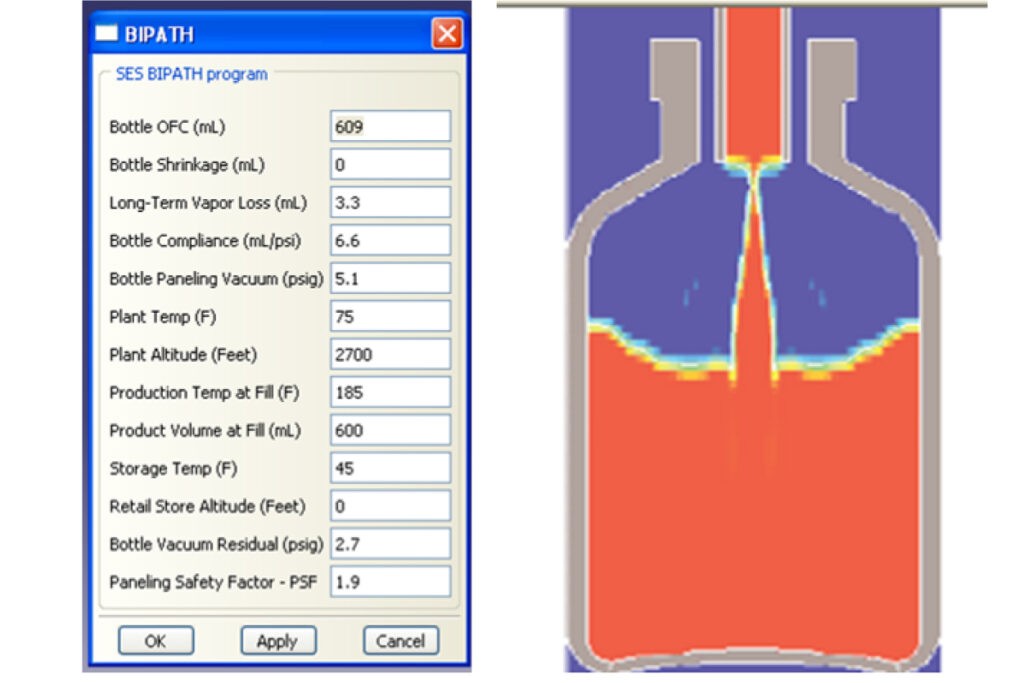
Figure 5b) Filling conditions predicted by a proprietary software tool, BIPATH, developed by Stress Engineering Services
Figure 5 Bottle-filling information
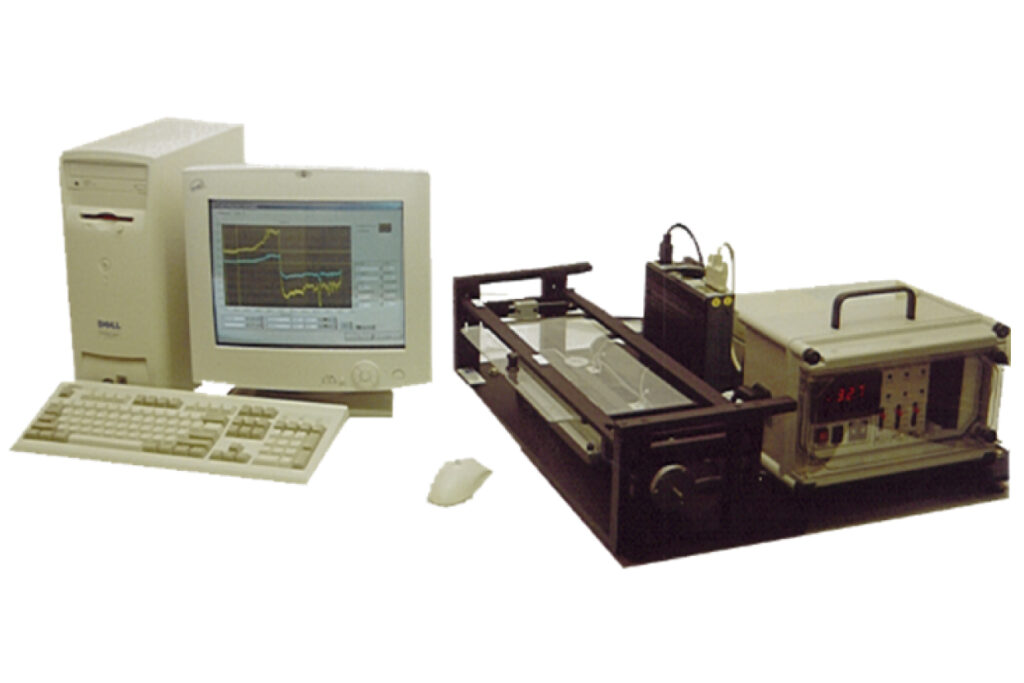
Figure 6a) Friction test apparatus
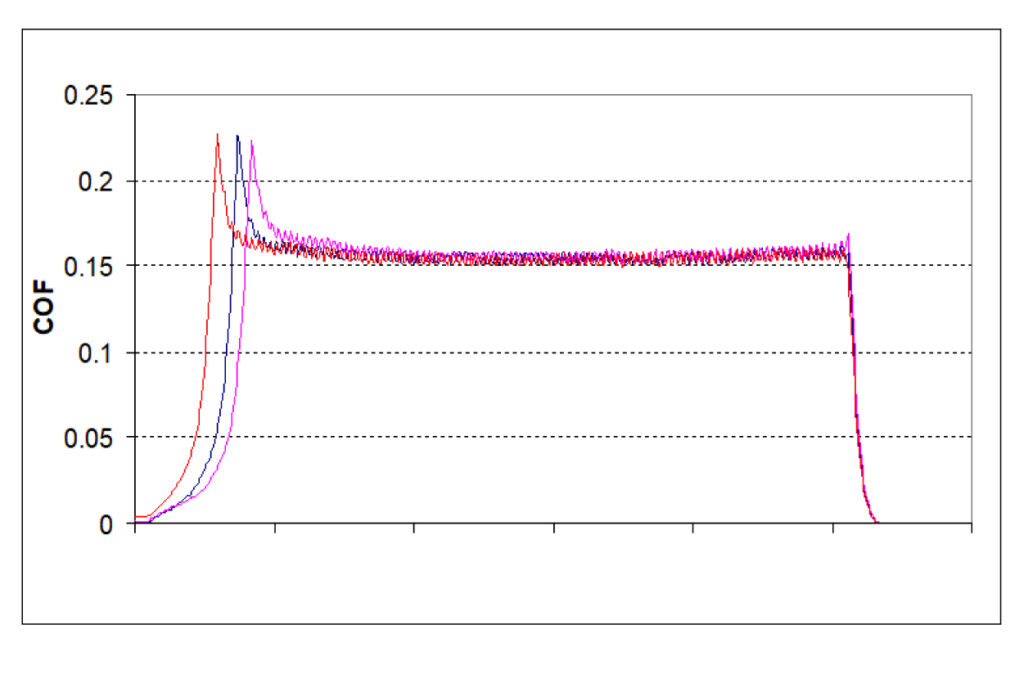
Figure 6b) Friction test results
Figure 6 Coefficient of friction (COF) testing
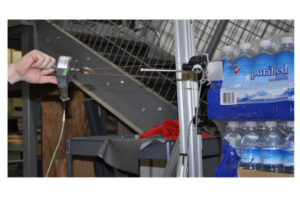
Figure 7a) Testing apparatus for on-site testing
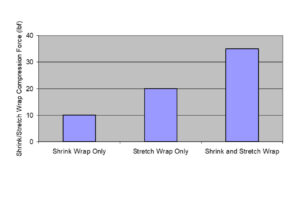
Figure 7b) Shrink and stretch wrap compression force test results
Figure 7 Shrink and stretch wrap compression testing
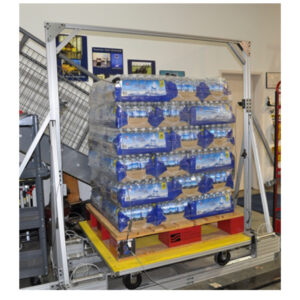
Figure 8a) PalletSled™ developed by Stress Engineering Services and ALOE Group to characterize and compare pallet-level packaging systems
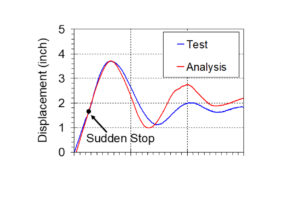
Figure 8b) Horizontal displacement at top layer of the unit load after a sudden stop
Figure 8 Transit vibration
Results
The analysis methods developed, and under continual refinement and expansion since the mid-1980’s by Stress Engineering Services and ALOE Group have proven to correctly predict the onset of damage as a function of primary and secondary loading conditions. This predictive approach enables the evaluation of new designs, or remediation of design problems without the need to resort to costly and time-consuming line trials. The modeling and simulation results (Figures 9 and 10) illustrate the accuracy of the methodology. The analysis not only correctly identifies the onset of bottle buckling, but it also predicts the buckling of the secondary tray package (Figures 9 and 10).
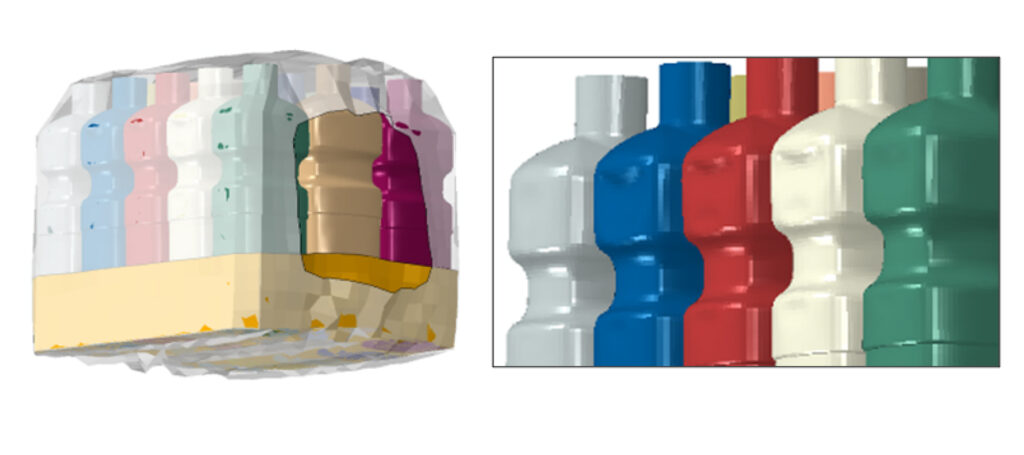
Figure 9a) Deformation of a compressed tray pack in a unit load
Figure 9 Primary package denting is properly identified
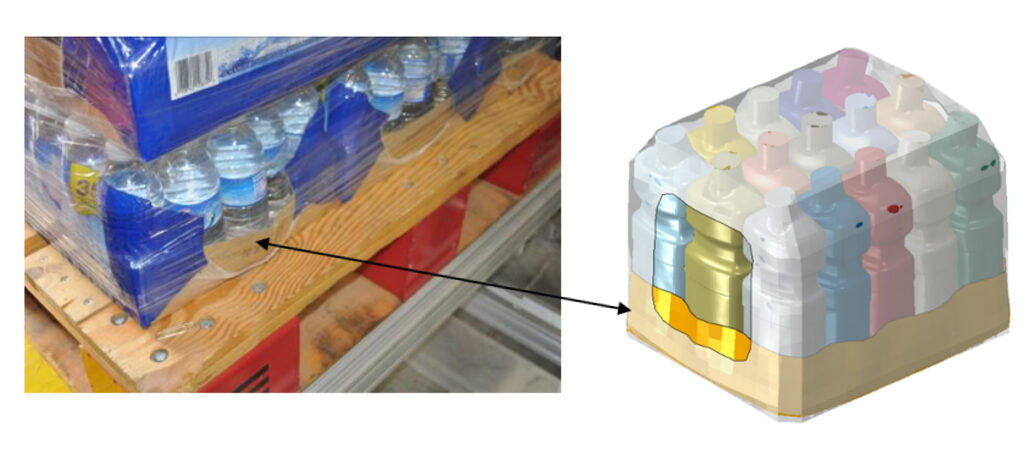
Figure 10 Secondary package (tray) buckling is properly identified
Democratization of Sustainable Package Development
A physics-based modeling, simulation, and analysis approach for tray-based unit load packaging was once only available to large organizations that could afford the investment. The remainder of the manufacturers were relegated to trial-and-error development. In the 15 years since the statement was made by the industry executive at the sustainability event (mentioned earlier), “democratization’ of modeling and simulation has become a significant trend in packaging engineering. [ The Path to Simulation Democratization | Engineering.com ] For packaging specifically, Stress Engineering Services and its package development firm, Force-4 (www.force-four.com), and logistics affiliate ALOE Group (www.aloegrp.com) are partnering with Amazon Web Services (AWS) to develop a “Sustainability Workbench” that will be available on the AWS cloud. The unique proprietary tools and capabilities of Stress Engineering will be available to help all packaging organizations accelerate their sustainability initiatives.
Ref: W006-SP-Improve Sustainability with Tray-Based Unit Loads
Keep in touch with us.
Sign up for our newsletter.